橡塑產(chǎn)品智能生產(chǎn)車間建設(shè)
立即咨詢
某公司為專業(yè)生產(chǎn)汽車橡膠配件的高新技術(shù)企業(yè),產(chǎn)品知名度高、產(chǎn)品暢銷海內(nèi)外,企業(yè)年產(chǎn)能達(dá)到1億件。但是,在當(dāng)前智能制造和大數(shù)據(jù)深度融合的趨勢(shì)下,傳統(tǒng)橡塑產(chǎn)品生產(chǎn)類企業(yè)暴露出了行業(yè)內(nèi)所存在的關(guān)鍵共性問題:對(duì)于車間的煉膠設(shè)備,需要依靠人工查看溫度、壓力、時(shí)間等參數(shù),無(wú)法對(duì)密煉次數(shù)和溫度、壓力變化等制造工藝參數(shù)進(jìn)行實(shí)時(shí)監(jiān)控與分析,導(dǎo)致了制造過程效率低下、產(chǎn)品整體質(zhì)量水平偏低的現(xiàn)象;橡塑的產(chǎn)品種類眾多、銷售量大,導(dǎo)致公司存在海量運(yùn)營(yíng)數(shù)據(jù),僅憑借管理人員的經(jīng)驗(yàn)判斷不能讓企業(yè)運(yùn)營(yíng)得高效而合理。
通過具體需求分析,項(xiàng)目將通過建設(shè)MES、PDM、DNC/MDC等企業(yè)信息化系統(tǒng),對(duì)該公司車間的生產(chǎn)過程進(jìn)行數(shù)字化和智能化改造,打造智能工廠,從而提高生產(chǎn)效率及產(chǎn)品質(zhì)量,最終實(shí)現(xiàn)過程協(xié)同和在線管控。
智能車間建設(shè)內(nèi)容主要包括以下幾個(gè)部分:現(xiàn)有設(shè)備智能化升級(jí)改造、車間互聯(lián)互通網(wǎng)絡(luò)架構(gòu)、制造過程現(xiàn)場(chǎng)數(shù)據(jù)采集與可視化、現(xiàn)場(chǎng)數(shù)據(jù)與生產(chǎn)管理軟件實(shí)現(xiàn)信息集成。總體方案架構(gòu)如下圖所示。
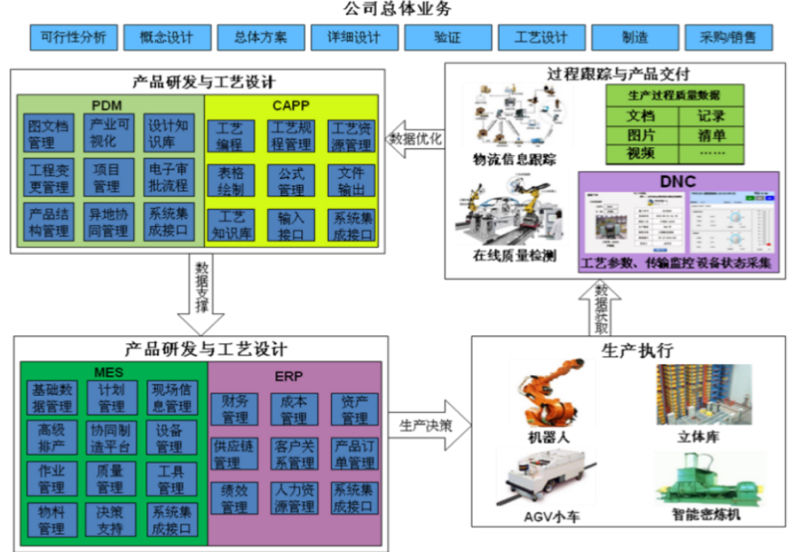
(一)現(xiàn)有設(shè)備智能化升級(jí)改造
針對(duì)智能化橡塑產(chǎn)品自動(dòng)生產(chǎn)線關(guān)鍵工序(密煉、配方)技術(shù)要求,在現(xiàn)有自動(dòng)化制造裝備的基礎(chǔ)上進(jìn)行升級(jí)改造,打造安全可控的核心智能制造裝備,形成全新的、智能化橡塑產(chǎn)品生產(chǎn)線;針對(duì)橡塑產(chǎn)品生產(chǎn)工藝和質(zhì)量檢測(cè)的要求,采用自主創(chuàng)新與集成創(chuàng)新相結(jié)合的新模式,建設(shè)安全可控的DCS分散式控制系統(tǒng)。
1.全自動(dòng)密煉機(jī)
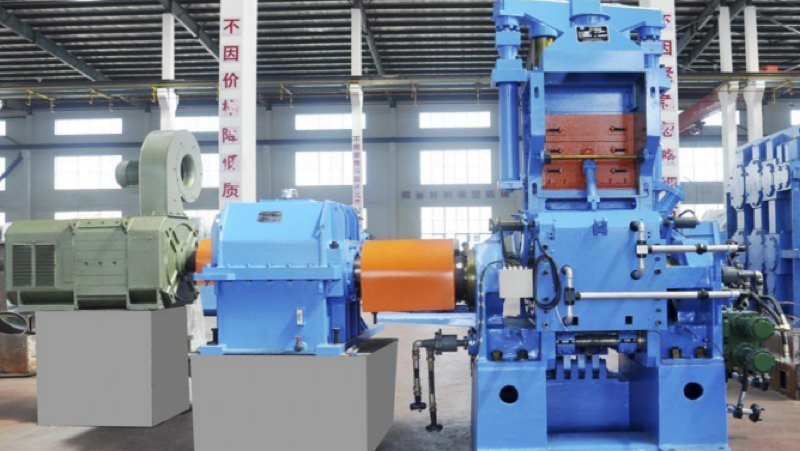
該設(shè)備用于根據(jù)公司配方煉制公司生產(chǎn)所需的橡膠原料。增加工位智能終端,接收生產(chǎn)任務(wù),同時(shí)將現(xiàn)有生產(chǎn)任務(wù)進(jìn)行情況匯報(bào)給生產(chǎn)管理人員;增加數(shù)據(jù)采集裝置,將密煉機(jī)的生產(chǎn)狀態(tài)實(shí)時(shí)傳送給設(shè)備監(jiān)控管理系統(tǒng)。同時(shí)定期提醒設(shè)備管理人員做維護(hù)或者故障分析;增加條碼掃描設(shè)備,根據(jù)不同物料批次,將生產(chǎn)的參數(shù)同生產(chǎn)原料綁定,支持產(chǎn)品追溯。
2. 磅秤系統(tǒng)
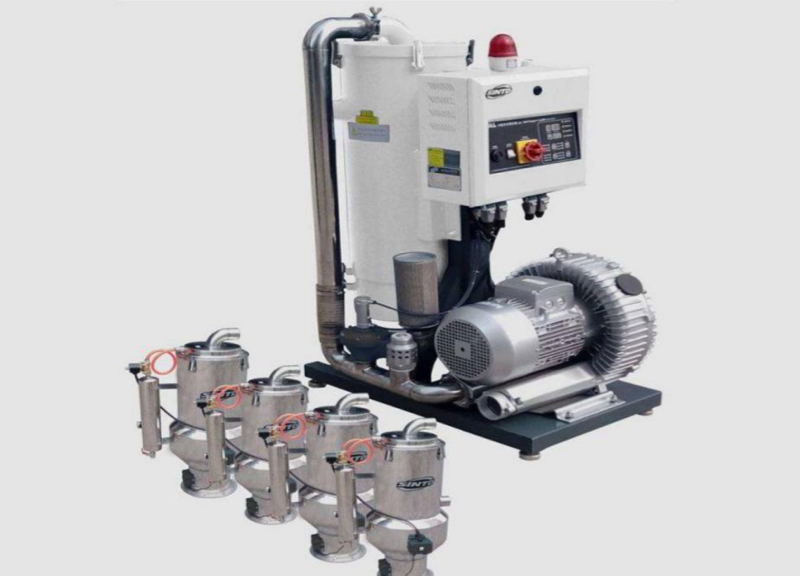
該設(shè)備用于控制原料進(jìn)入密煉機(jī)的質(zhì)量,完成配方標(biāo)準(zhǔn)執(zhí)行。增加工位智能終端,接收生產(chǎn)配方,同時(shí)將現(xiàn)有生產(chǎn)任務(wù)進(jìn)行情況匯報(bào)給生產(chǎn)管理人員;增加數(shù)據(jù)采集裝置,將配方磅秤的生產(chǎn)數(shù)據(jù)實(shí)時(shí)傳送給設(shè)備監(jiān)控管理系統(tǒng)。同時(shí)定期提醒設(shè)備管理人員做維護(hù)或者故障分析;增加條碼掃描設(shè)備,根據(jù)不同物料批次,將生產(chǎn)的參數(shù)同生產(chǎn)原料綁定,支持產(chǎn)品追溯;將配方管理系統(tǒng)集成到MES,同生產(chǎn)管理系統(tǒng)協(xié)同制造。
3.上輔機(jī)系統(tǒng)
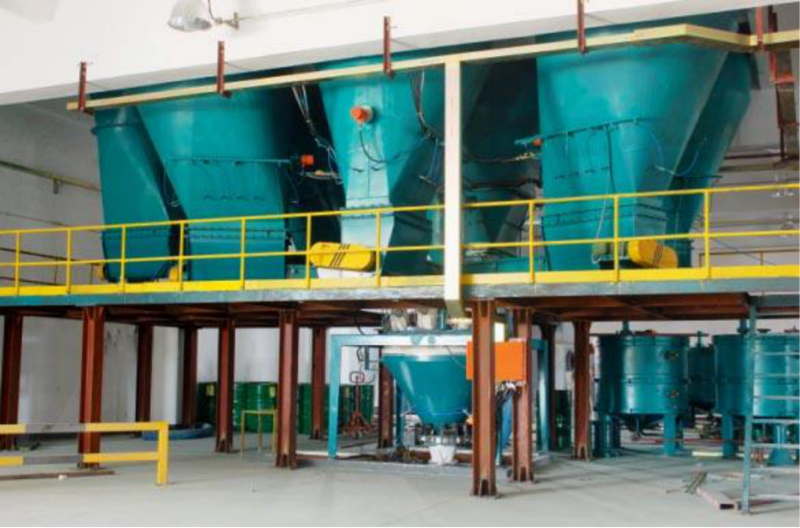
該設(shè)備用于密煉原材料供給。增加工位智能終端,接收生產(chǎn)配方,同時(shí)將現(xiàn)有生產(chǎn)任務(wù)進(jìn)行情況匯報(bào)給生產(chǎn)管理人員;增加數(shù)據(jù)采集裝置,將配方磅秤的生產(chǎn)數(shù)據(jù)實(shí)時(shí)傳送給設(shè)備監(jiān)控管理系統(tǒng)。同時(shí)定期提醒設(shè)備管理人員做維護(hù)或者故障分析;增加條碼掃描設(shè)備,根據(jù)不同物料批次,將生產(chǎn)的參數(shù)同生產(chǎn)原料綁定,支持產(chǎn)品追溯。
4. DCS分散式控制系統(tǒng)
建設(shè)分散式控制系統(tǒng)(DCS),用以對(duì)橡塑產(chǎn)品生產(chǎn)線設(shè)備進(jìn)行分散控制與集中監(jiān)控,完成數(shù)字化車間的建設(shè)工作。DCS系統(tǒng)網(wǎng)絡(luò)架構(gòu)如下圖所示。
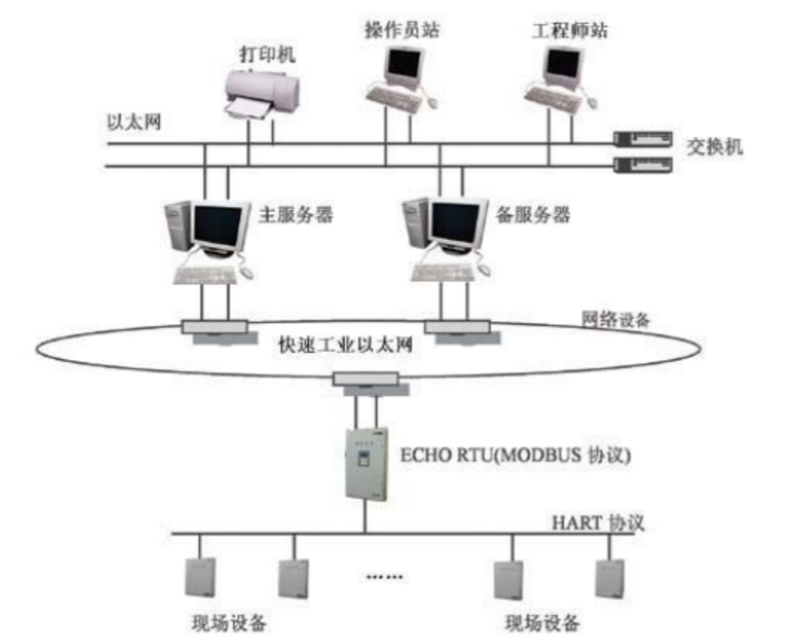
在過程控制級(jí),分別對(duì)現(xiàn)場(chǎng)設(shè)備進(jìn)行單機(jī)控制,并在此基礎(chǔ)上,采用工業(yè)以太網(wǎng)將各條生產(chǎn)線聯(lián)接起來,通過上位工控機(jī)進(jìn)行監(jiān)控,構(gòu)成生產(chǎn)監(jiān)控級(jí),從而形成基于現(xiàn)場(chǎng)總線和工業(yè)以太網(wǎng)的DCS系統(tǒng)。整個(gè)控制系統(tǒng)貫穿了現(xiàn)場(chǎng)設(shè)備層、車間監(jiān)控層和工廠管理層。
(二)車間互聯(lián)互通網(wǎng)絡(luò)架構(gòu)與信息模型
1.車間互聯(lián)互通網(wǎng)絡(luò)架構(gòu)與信息模型
以MES系統(tǒng)為基礎(chǔ),綜合考慮企業(yè)數(shù)字化車間建設(shè)基礎(chǔ)以及裝備制造行業(yè)建設(shè)的共性需求,進(jìn)行集成開發(fā),對(duì)已有管理信息化系統(tǒng)及即將實(shí)施的系統(tǒng)(ERP、PDM、CAPP等)、自動(dòng)化裝備(密煉機(jī)、上輔機(jī)、配方磅秤等)進(jìn)行集成,實(shí)現(xiàn)對(duì)設(shè)備、生產(chǎn)、物流的集成應(yīng)用,從而搭建車間互聯(lián)互通網(wǎng)絡(luò)架構(gòu)與信息模型,建立數(shù)字化車間集成平臺(tái)。
2.根據(jù)精忠橡塑需求開發(fā)模塊化信息模型
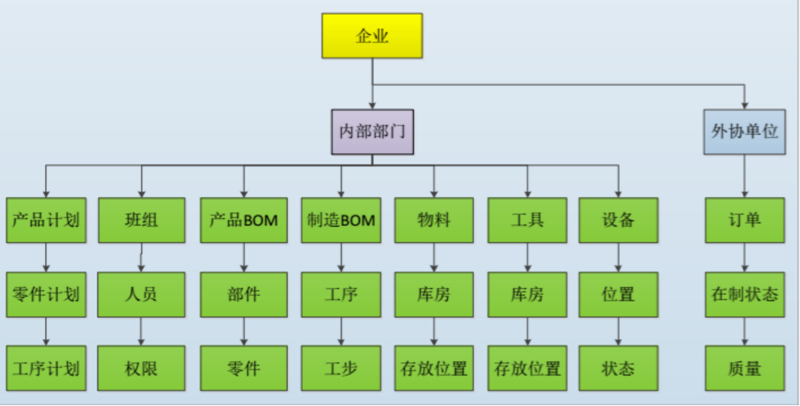
(三)制造過程現(xiàn)場(chǎng)數(shù)據(jù)采集與可視化
1.制造過程現(xiàn)場(chǎng)數(shù)據(jù)采集與可視化
公司建設(shè)制造過程采集與分析系統(tǒng),通過對(duì)制造過程現(xiàn)場(chǎng)數(shù)據(jù)全方位的信息采集,并實(shí)現(xiàn)可視化,高效統(tǒng)一的實(shí)施產(chǎn)品質(zhì)量一致性管理,采取自動(dòng)化手段實(shí)現(xiàn)在線、實(shí)時(shí)的質(zhì)量檢測(cè)、分析、顯示和預(yù)警。
2.系統(tǒng)的功能、架構(gòu)以及數(shù)據(jù)集成
通過建設(shè)制造過程采集與分析系統(tǒng),以及與MES系統(tǒng)的無(wú)縫集成,實(shí)現(xiàn)產(chǎn)品生產(chǎn)和質(zhì)量全過程控制的動(dòng)態(tài)管理。通過對(duì)各個(gè)產(chǎn)品的質(zhì)量規(guī)劃、實(shí)時(shí)采集、動(dòng)態(tài)分析、在線檢測(cè)和預(yù)警功能,達(dá)到制造過程中的產(chǎn)品質(zhì)量信息的準(zhǔn)確掌握,加強(qiáng)實(shí)時(shí)現(xiàn)場(chǎng)管控能力,減少錯(cuò)誤、提高效率、穩(wěn)定制造過程。
系統(tǒng)整體上由四部分組成,依次分別為數(shù)據(jù)采集器、一體化生產(chǎn)線數(shù)據(jù)采集系統(tǒng)、采集與控制應(yīng)用服務(wù)器和監(jiān)控客戶端。如下圖所示,圖中右側(cè)區(qū)域?yàn)镸ES系統(tǒng),制造過程采集與分析系統(tǒng)與MES系統(tǒng)通過數(shù)據(jù)庫(kù)實(shí)現(xiàn)業(yè)務(wù)互通。
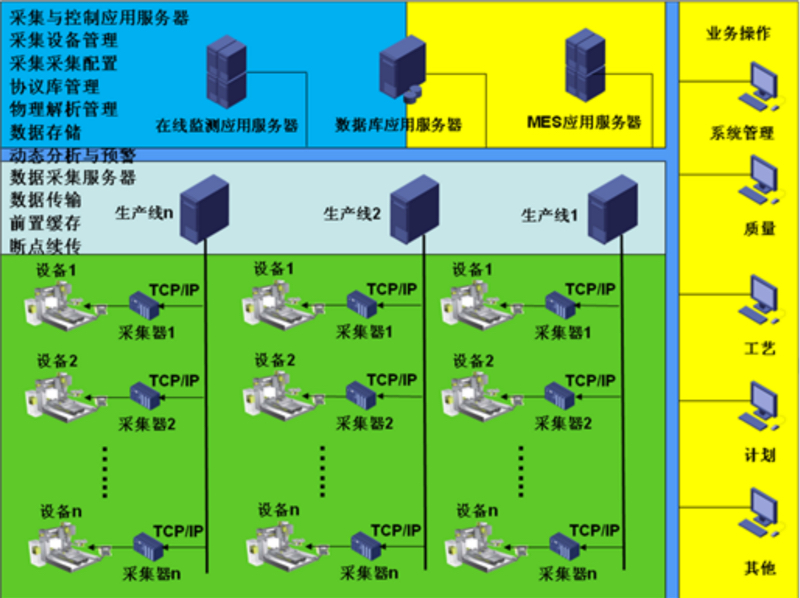
3.數(shù)據(jù)采集及可視化
通過對(duì)設(shè)備進(jìn)行監(jiān)控,采集制造過程現(xiàn)場(chǎng)數(shù)據(jù),將生產(chǎn)計(jì)劃與設(shè)備加工過程中的實(shí)時(shí)溫度信息、壓力等信息進(jìn)行緊密關(guān)聯(lián),從中發(fā)掘現(xiàn)有加工過程中的瓶頸問題,進(jìn)一步支撐企業(yè)的精益改進(jìn)。
(四)現(xiàn)場(chǎng)數(shù)據(jù)與生產(chǎn)管理軟件實(shí)現(xiàn)信息集成
與ERP、CAPP系統(tǒng)集成,MES系統(tǒng)定時(shí)讀取ERP系統(tǒng)及CAPP系統(tǒng)中的任務(wù)數(shù)據(jù),同步到MES系統(tǒng)數(shù)據(jù)庫(kù)中。